For more than 25 years Pörner Grimma has been liaising with renowned European licensors and experienced partners to build plants for the formaldehyde product family as an EPCM contractor.
In close cooperation with Dynea, the longtime licensing partner, the silver catalyst process for the production of formalin has been constantly improved to become the best of its kind. Technical and economic comparisons of several international clients as well as the experience from joint design and construction of more than 10 plants in the last years prove this.
As an EPC contractor Pörner sells, designs and builds plants of the formaldehyde technology family. Together with international licensors and technology partners Pörner Grimma can offer the following production plants with offsite, utilities and infrastructure units:
- FORMALDEHYDE production based on Silver Catalyst and Metal Oxide Catalyst
- UFC (Urea formaldehyde precondensate) production based on Silver Catalyst and Metal Oxide Catalyst
- PARAFORMALDEHYDE production
- HEXAMINE (Hexamethylenetetramine) production, Liquid Phase and Gaseous Phase Process
- PENTA (Pentaerythritol) production
- ACETALDEHYDE production from ethanol
- GLUES and RESINS (UF, MF, MUF, PF, Epoxy, Alkyd, Polyester, Novolaks, Powder Bakelite) production
Formaldehyde
Formaldehyde is one of the most important organic raw materials in the chemical industry. Formaldehyde is an important raw material for the chemical industry and the basis for many industrial products. More than 50 branches of industry using formaldehyde and its derivatives, as adhesives, resins, and in many other applications. The global annual consumption of formaldehyde is about 41 million tons. 51% of them are made in China.
Pöerner Grimma is not only a specialist in the formaldehyde method, but also for process applications of formaldehyde derivatives. Technically formaldehyde can be produced by the catalytic oxidation of methanol. These are, two methods, the silver and the metal oxide method.
Although the catalyst has to be changed frequently in the silver method, but the aqueous formaldehyde solution is of higher quality because the formic acid content is lower.
Silver Catalyst Process
The Silver Catalyst process is the most safe process of formaldehyde production. Formaldehyde concentration and residue methanol produced with the Silver Catalyst Process is as good as from best metal oxide process. Less formic acid and no caustic soda and antifoam agent makes the product more versatile for all formulations and customers.
There is also no hot oil used in this process, just water/steam and this reduces the fire risk. There is no oxygen in the absorber, this not only reduces the fire risk but improves the product quality as well.
The catalyst can be removed without dust and waste in a few hours. Re-catalization can take less than 24 hours so only small holding tanks are necessary to serve customers during re-catalization.
The investment costs for the Silver Catalyst Process are similar compared to the Metal Oxide Process but there are other advantages to this system:
- the catalyst is inexpensive because it is fully regenerated,
- there is less electricity consumption,
- higher steam generation and less cooling demand.
These factors more than compensate for the slightly higher methanol consumption compared to the Metal Oxide Process.
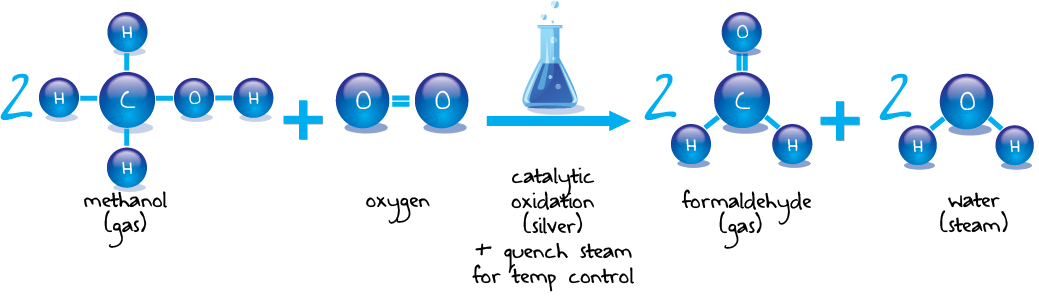
The process
- An evaporated Methanol Water Mixture is fed together with ambient air to the silver catalyst. The generated process gas is than absorbed in water and condensed in a selective absorption step.
- Standard trade solutions up to 49 % w/w formaldehyde with 1-2 % w/w methanol are produced without distillation.
- Alternatively we offer the special tail gas recycling technology to achieve high concentrated formaldehyde solutions up to 55 % w/w formaldehyde with 0,5 -1 % w/w methanol without distillation.
- The H2-rich absorption tail gas is combusted in a thermal oxidizer or special boiler and is generating steam or can even be fed to a gas motor generating electric power.
Metal Oxide Process
The Metal Oxide Process yields better quantities of formaldehyde therefore there is slightly less consumption of methanol. It also has similar investment costs to the Silver Catalyst Process.
Our process also allows the free choice of catalyst supplier as Pöerner and its licensor are independent companies with the client’s wishes at heart. The final decision on which process to choose depends on the individual client and their needs.
Factors that influence this decision include costs of raw materials, utility costs, catalyst costs and safety and operation aspects etc.
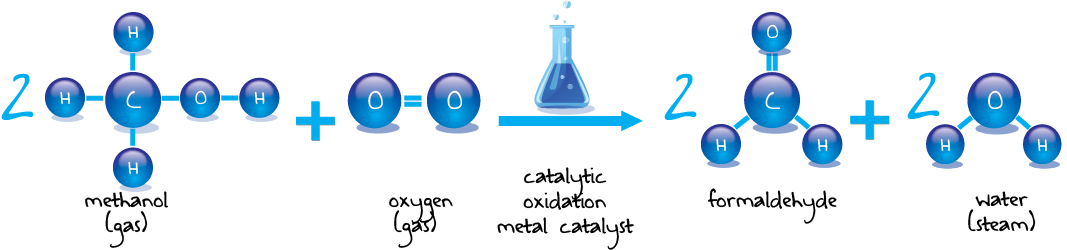
The Process
- Methanol is fed together with ambient air to the metal oxide catalyst (iron oxide in combination with molybdenum and/or vanadium).
- The generated process gas is than absorbed in water and condensed in an absorption step.
- About one thrid of the absorption off gas is recycled to the reactor. Formaldehyde solutions up to 55 % w/w formaldehyde with 0,5 -1 % w/w methanol are produced.
- The absorption off gas is oxidized on a palladium catalyst which can be equipped alternatively with waste heat recovery.
fasil Technology
Dynea, one of the world’s leading manufacturers of formaldehyde, has decades of experience and has developed its own proprietary process, the silver catalyst-formaldehyde technology – fasil ™.
fasil ™ is the safest and most environmentally friendly formaldehyde process on the market. Catalyst research and development as well as feedback from the operational area guarantee formaldehyde production at the lowest total cost of ownership. fasil ™ is the preferred option for first-class customers looking for a safe, bespoke, low-cost concentrate-formaldehyde process.
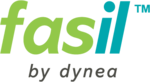
Formaldehyde derivatives
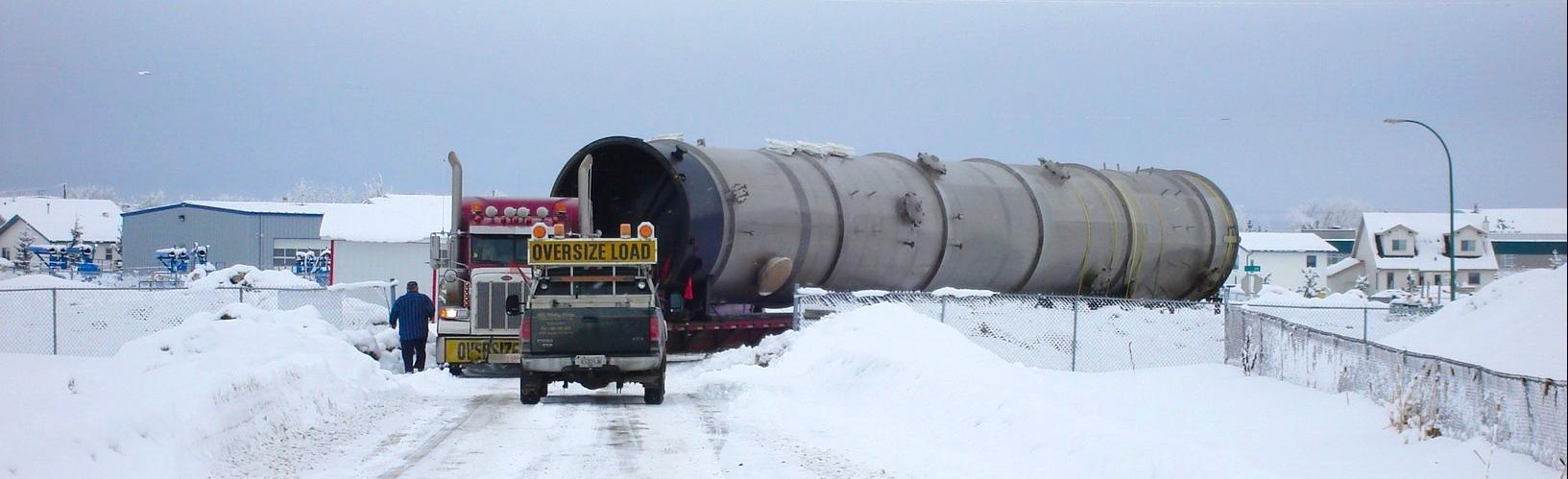
Formaldehyde is an important raw material for the chemical industry and is used to manufacture many industrial and consumer products. Over 50 branches of industry now use formaldehyde and its derivatives in glues and resins and many other industrial applications. Because Pöerner Grimma is the specialist in process design for Formaldehyde, we also specialize in the process design for formaldehyde derivatives. These derivatives are used for many different applications across industry and households.
They include:
- UFC
- Paraformaldehyde
- Hexamine
- Penta
- Acetaldehyde from Ethanol
- Glues and resins
Precondensate (UFC)
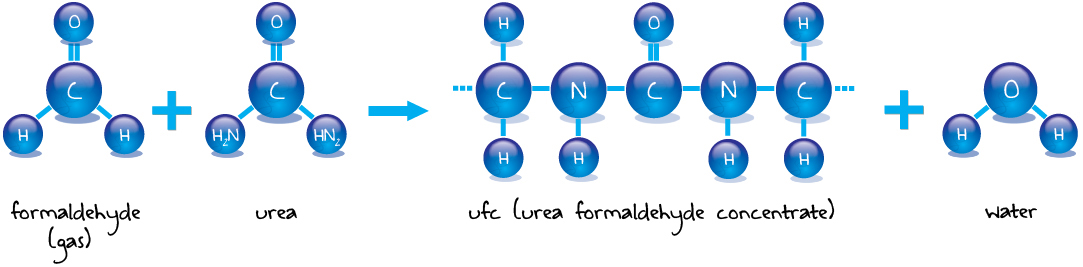
Silver catalyst process
- An evaporated Methanol Water Mixture is fed together with ambient air to the silver catalyst.
- The generated process gas is then absorbed in a Urea-Water solution and condensed in a selective absorption step.
- Standard trade solutions of up to UFC 75 can be produced directly in the absorber. Higher concentrations are not achievable due to process water balance.
- The H2 rich absorption tail gas is combusted in a thermal oxidizer or special boiler and is generating steam or can even be fed to a gas motor generating electric power.
Metal oxide process
- Methanol is fed together with ambient air to the metal oxide catalyst (iron oxide in combination with molybdenum and/or vanadium).
- The generated process gas is then absorbed in a Urea-Water solution and condensed in a selective absorption step
- About two thirds of the absorption off gas is recycled to the reactor
- The absorption off gas is oxidized on a palladium catalyst which can be equipped alternatively with waste heat recovery.
- All standard trade solutions of up to UFC 85 can be produced.
Paraformaldehyd
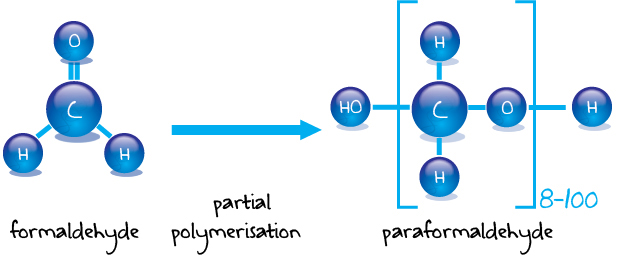
- The Formaldehyde solution is concentrated by evaporation. Depending on the feed concentration two or three evaporation steps are required.
- The concentrated solution is then congealed and subsequently dried according to the various product specifications
- The paraformaldehyde that is produced is made up of white, free flowing granules or prills with a Formaldehyde content of 91 – 98 % w/w with the ideal being 95 ± 1 % w/w
- Key features of the product are:
- high reactivity
- excellent solubility
- very good storage properties
Hexamethylentetramine (hexamine or urotropin)
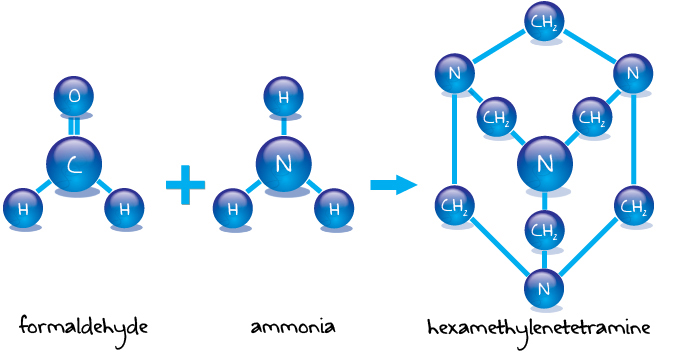
Hexamine liquid phase process
- Liquid Ammonia is evaporated and fed into the reactor system where it reacts with a formaldehyde solution to hexamine molecules which are dissolved in a mother-liquor
- The Mother-liquor is fed to a crystallization unit where the hexamine crystals are formed
- The hexamine crystals are separated in a centrifuge and the hexamine is subsequently dried in a fluidized bed drier.
- The residue mother-liquor from the centrifuge is recirculated to the reactor
- Key features of the product are:
- pure white and crystalline structure
- very good flow characteristics
- stabilization with SiO2 is possible
Hexamine gaseous phase process
- Liquid Ammonia is evaporated and feed into the reactor system where it reacts with the formaldehyde gas from the formaldehyde reactor to hexamine molecules which are dissolved in a mother-liquor
- The Mother-liquor is fed to a crystallization unit where the hexamine crystals are formed
- The hexamine crystals are separated in a centrifuge and the hexamine is subsequently dried in a fluidized bed drier
- The residue liquor from the centrifuge is recirculated to the reactor
- Key features of the product are:
- pure white and crystalline structure
- very good flow characteristics
- stabilization with SiO2 is possible
Pentaerythritol (penta)

- Acetaldehyde and Formaldehyde solution react in a continuous process in a first step under alkaline conditions (Aldol Condensation) and in a second reaction step it reacts with formaldehyde (Cannizzaro Reaction) to complete the synthesis of Penta
- The reaction product is fed to a continuous crystallization unit
- Di-Pentaerythritol can also be produced as secondary product
- Sodium Formate is formed as a by-product
- Key features of the continuous process are:
- low formation of unwanted by-products
- low and constant utility demand
- excellent operation results in small apparatuses
Acetaldehyde (aceta)
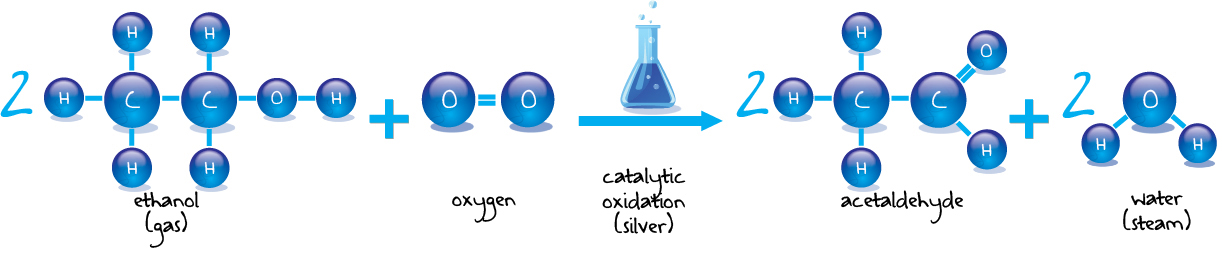
Ethanol process:
- Evaporated Ethanol is fed together with ambient air to the silver catalyst. The generated process gas is than absorbed in water and condensed.
- The generated solution is than fed to the Acetaldehyde distillation unit where the pure acetaldehyde product of the desired concentration is produced.
- The sump product of the acetaldehyde distillation which is left unreacted – ethanol and water – is fed to the Ethanol distillation step where the ethanol is recovered as head product and recycled to the reaction section
- The sump product of the Ethanol distillation is mainly used as absorption water in the absorption unit, only a small quantity is discharged as waste water
- The H2-rich absorption tail gas can be thermal oxidized and the generated heat can be utilized for steam generation.
Glues and resins
Glues and resin plants designed and supplied by Pörner are tailor adapted and optimized production units for a broad range of products.
The product groups that Pörner caters for are:
- Urea formaldehyde resins (UF), melamine formaldehyde resins (MF) and melamine urea resins (MUF) production plants
- Phenol formaldehyde resins (PF) production plants
- Epoxy resins production plants
- Alkyd and polyester resins production plants
- Glue production plants
- Novolak and Resol production units
- Powder Bakelite production units