Increasingly efficient industrial plants require high-quality lubricants. Hard and soft waxes to be used for the production of food and cosmetics are in great demand.
Due to sophisticated processing technologies (e. g. catalytic cracking) refineries produce less by-products such as aromatics and paraffin/waxes. For this reason lube oil and paraffin producers look for new, more efficient technologies.
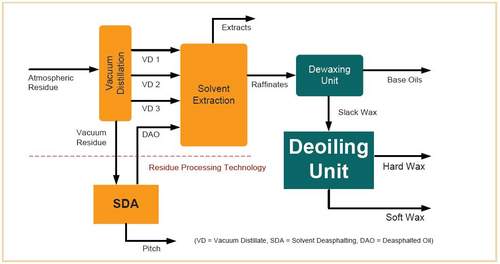
For optimum processing of feeds having different properties, EDL and Sulzer offer dewaxing and deoiling technologies with and without solvent. The selection of the optimal process guarantees the best possible product quality and the most attractive investment.
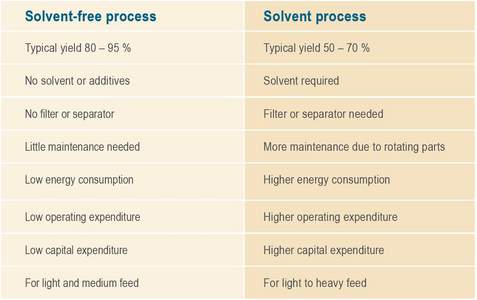
our approach to an optimized technology: experience, tests and simulation
The tests show the following results:
- Determination of the equilibrium data
- Optimization and determination of process parameters (crystallization temperature, solvent ratio, temperature gradients, …)
- Determination of lube oil, soft wax and hard wax yield
- Analytical evaluation of the product quality
The test results are the basis for process simulation as well as for:
- Thermodynamic process design
- Determination of substance properties for further processing
- Design and dimensioning of a complete dewaxing/deoiling plant incl. required off-sites
EDL and Sulzer offer the most efficient solution – the free selection of the process (with or without solvent) or a combination of both technologies. Plant modernization and capacity increase are possible without production downtime by combining the processes.